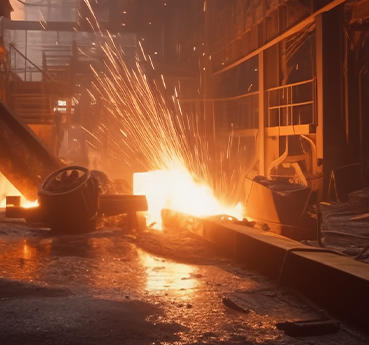
آهنگری یک روش فرآوری است که از ماشین آلات آهنگری برای اعمال فشار به شمشهای فلزی استفاده میکند و باعث میشود آنها تحت تغییر شکل پلاستیکی قرار گیرند تا آهنگری با خواص مکانیکی، شکلها و اندازههای خاص به دست آید. یکی از دو جزء اصلی آهنگری ( آهنگری و مهر زنی ) است. آهنگری می تواند نقص هایی مانند تخلخل ریخته گری در فرآیند ذوب فلزات را از بین ببرد، ریزساختار را بهینه کند، و به دلیل حفظ خطوط جریان کامل فلز، خواص مکانیکی آهنگری عموماً بهتر از ریخته گری های همان مواد است. قطعات مهم در ماشین آلات مرتبط با بارهای زیاد و شرایط کاری سخت، به جز اشکال ساده که می توانند به صورت صفحات، پروفیل یا قطعات جوش داده شوند، بیشتر از آهنگری ساخته می شوند.
دمای تغییر شکل مواد آهنگری
دمای شروع تبلور مجدد فولاد با 800 ℃ تقسیم می شود، با آهنگری داغ بالای 800 ℃. آهنگری بین 300 تا 800 درجه سانتیگراد را فورج گرم یا آهنگری نیمه گرم و آهنگری در دمای اتاق را آهنگری سرد می گویند. آهنگری های مورد استفاده در بیشتر صنایع فورج گرم هستند، در حالی که آهنگری گرم و سرد عمدتاً برای آهنگری قطعاتی مانند خودرو و ماشین آلات عمومی استفاده می شود. آهنگری گرم و سرد می تواند به طور موثر مواد را ذخیره کند.
دسته آهنگری
با توجه به دمای آهنگری، می توان آن را به آهنگری گرم، آهنگری گرم و آهنگری سرد تقسیم کرد.
با توجه به مکانیسم شکل دهی، آهنگری را می توان به آهنگری آزاد، آهنگری قالب، نورد حلقه و آهنگری ویژه تقسیم کرد.
1. آهنگری رایگان. روش فرآوری آهنگری به استفاده از ابزار ساده جهانی یا اعمال مستقیم نیروهای خارجی بین سندان بالایی و پایینی تجهیزات آهنگری برای تغییر شکل بیلت و به دست آوردن شکل هندسی و کیفیت داخلی مورد نیاز است. آهنگری که با روش آهنگری آزاد تولید می شود، آهنگری آزاد نامیده می شود. آهنگری آزاد عمدتاً دسته های کوچک آهنگری را تولید می کند و از تجهیزات آهنگری مانند چکش و پرس های هیدرولیک برای شکل دادن و پردازش قطعات و به دست آوردن آهنگرهای واجد شرایط استفاده می کند. فرآیندهای اساسی آهنگری آزاد شامل برهم زدن، ازدیاد طول، پانچ، برش، خمش، پیچش، جابجایی و آهنگری است. آهنگری رایگان از روش فورج گرم استفاده می کند.
2. قالب جعل. فورج قالب را می توان به فورج قالب باز و فورج قالب بسته تقسیم کرد. بیلت های فلزی با تغییر شکل فشاری در محفظه قالب آهنگری با شکل خاصی برای به دست آوردن آهنگری تشکیل می شوند. فورج قالب به طور کلی برای تولید قطعات با وزن های کوچک و اندازه های دسته ای بزرگ استفاده می شود.
فورج قالب را می توان به فورج قالب داغ، فورج گرم و آهنگری سرد تقسیم کرد. آهنگری گرم و آهنگری سرد مسیرهای توسعه آتی آهنگری قالب هستند و همچنین نشان دهنده سطح فناوری آهنگری هستند. با توجه به طبقه بندی مواد، آهنگری قالب را می توان به آهنگری قالب فلزی سیاه، آهنگری قالب فلزی غیر آهنی و تشکیل محصول پودری تقسیم کرد. همانطور که از نام آن پیداست، این مواد فلزات سیاه رنگ مانند فولاد کربنی، فلزات غیرآهنی مانند مس و آلومینیوم و مواد متالورژی پودر هستند. اکستروژن باید متعلق به فورج قالب باشد و می تواند به اکستروژن فلزات سنگین و اکستروژن فلز سبک تقسیم شود. لازم به ذکر است که بیلت نمی تواند کاملاً محدود شود. بنابراین، کنترل دقیق حجم بیلت، کنترل موقعیت نسبی قالب آهنگری و اندازه گیری آهنگری، تلاش برای کاهش سایش قالب آهنگری ضروری است.
3. حلقه آسیاب. رولینگ حلقه ای به تولید قطعات دایره ای شکل با قطرهای مختلف با استفاده از تجهیزات تخصصی مانند دستگاه های نورد حلقه ای گفته می شود و همچنین برای تولید قطعات چرخ مانند چرخ خودرو و چرخ قطار استفاده می شود.
4. آهنگری مخصوص. آهنگری ویژه شامل روش های آهنگری مانند فورج رول، نورد متقاطع گوه ای، آهنگری شعاعی و آهنگری قالب مایع است که همگی برای تولید قطعات خاص با شکل خاص مناسب تر هستند.
به عنوان مثال، فورج رول می تواند به عنوان یک فرآیند آماده سازی موثر عمل کند و فشار شکل دهی بعدی را به میزان قابل توجهی کاهش دهد. نورد متقاطع گوه ای می تواند قطعاتی مانند توپ های فولادی و شفت های انتقال تولید کند. آهنگری شعاعی می تواند آهنگری های بزرگی مانند لوله تفنگ و میل پله ای تولید کند.
جعل می میرند
با توجه به حالت حرکت قالب آهنگری، آهنگری را می توان به آهنگری نوسانی، آهنگری چرخشی نوسانی، آهنگری رول، نورد متقاطع گوه ای، نورد حلقه ای و نورد مورب تقسیم کرد. آهنگری چرخشی، آهنگری چرخشی و آهنگری دقیق نیز می تواند برای حلقه پرس هیدرولیک آهنگری هوانوردی سنگین 400MN (40000 تن) در چین استفاده شود. برای بهبود میزان استفاده از مواد، فورج رول و نورد متقاطع را می توان به عنوان فرآیندهای قبلی برای پردازش مواد باریک استفاده کرد. آهنگری دوار نیز مانند آهنگری آزاد به صورت موضعی شکل می گیرد و مزیت آن این است که می توان آن را حتی تحت نیروهای آهنگری کوچکتر نسبت به اندازه آهنگری تشکیل داد. این روش آهنگری، از جمله آهنگری آزاد، شامل انبساط مواد از مجاورت سطح قالب به سطح آزاد در حین پردازش است که اطمینان از دقت را دشوار می کند. بنابراین، با کنترل جهت حرکت قالب آهنگری و فرآیند آهنگری چرخشی با کامپیوتر، می توان محصولات پیچیده و با دقت بالا را با نیروی آهنگری کمتر به دست آورد، مانند تولید آهنگری با انواع مختلف و اندازه های بزرگ پره های توربین بخار. .
حرکت قالب و درجات آزادی تجهیزات آهنگری متناقض است. با توجه به ویژگی های محدودیت های تغییر شکل در مرکز مرده پایین، تجهیزات آهنگری را می توان به چهار شکل زیر تقسیم کرد:
1. فرم نیروی آهنگری محدود: یک پرس هیدرولیک که مستقیماً لغزنده را با فشار روغن به حرکت در می آورد.
2. روش محدودیت شبه ضربه ای: پرس هیدرولیکی که مکانیزم شاتون میل لنگ را با فشار هیدرولیک به حرکت در می آورد.
3. روش محدودیت ضربه: یک پرس مکانیکی با میل لنگ، شاتون و مکانیسم گوه ای که لغزنده را به حرکت در می آورد.
4. روش محدودیت انرژی: از مکانیزم مارپیچ پیچ و پرس اصطکاکی استفاده کنید. برای دستیابی به دقت بالا در هنگام تست گرم پرس های هیدرولیک آهنگری هوانوردی سنگین، باید به جلوگیری از اضافه بار در نقطه مرگ پایین، کنترل سرعت و موقعیت قالب توجه شود. زیرا اینها بر روی تحمل، دقت شکل و عمر آهنگری تاثیر خواهند داشت. علاوه بر این، برای حفظ دقت، باید به تنظیم فاصله بین ریل های راهنمای لغزنده، اطمینان از سفتی، تنظیم نقطه مرده پایین تر و استفاده از دستگاه های انتقال کمکی توجه شود.
نوار لغزنده جعلی
لغزنده های آهنگری را می توان به حرکات عمودی و افقی تقسیم کرد (برای آهنگری قطعات باریک، روانکاری، خنک سازی و آهنگری قطعات تولیدی با سرعت بالا استفاده می شود) و از دستگاه های جبران برای افزایش حرکت در جهات دیگر استفاده می شود. روشهای بالا متفاوت هستند و نیروی آهنگری، فرآیند، میزان استفاده از مواد، خروجی، تحمل ابعادی، و روش روانکاری و خنککاری مورد نیاز برای جعل موفقیتآمیز محصول نوع دیسک بزرگ، همگی متفاوت هستند. این عوامل نیز عواملی هستند که بر سطح اتوماسیون تأثیر می گذارند.مواد مورد استفاده برای آهنگری
مواد اصلی مورد استفاده برای آهنگری فولاد کربن و فولاد آلیاژی با ترکیبات مختلف و به دنبال آن آلومینیوم، منیزیم، مس، تیتانیوم و آلیاژهای آنها می باشد. حالت اولیه مواد شامل میله ها، شمش ها، پودرهای فلزی و فلزات مایع است. نسبت سطح مقطع فلز قبل از تغییر شکل به سطح مقطع بعد از تغییر شکل را نسبت آهنگری می گویند. انتخاب صحیح نسبت آهنگری، دمای مناسب گرمایش و زمان عایق کاری، دمای مناسب اولیه و نهایی آهنگری، مقدار تغییر شکل معقول و سرعت تغییر شکل ارتباط نزدیکی با بهبود کیفیت محصول و کاهش هزینه ها دارد. به طور کلی، آهنگری های کوچک و متوسط از میله های گرد یا مربع به عنوان بیلت استفاده می کنند. ساختار دانه و خواص مکانیکی مواد میله یکنواخت و خوب، با شکل و اندازه دقیق، کیفیت سطح خوب و تولید انبوه با سازماندهی آسان است. تا زمانی که دمای گرمایش و شرایط تغییر شکل به طور معقولی کنترل شود، آهنگرهای با عملکرد بالا را می توان بدون تغییر شکل قابل توجه آهنگری جعل کرد. شمش فقط برای آهنگری های بزرگ استفاده می شود. شمش ساختاری به شکل ریختهگری با کریستالهای ستونی بزرگ و مرکز شل است. بنابراین، لازم است بلورهای ستونی را از طریق تغییر شکل پلاستیکی بزرگ به دانه های ریز شکسته و آنها را آزادانه فشرده کنیم تا ساختار فلزی و خواص مکانیکی به دست آید. پریفرم های متالورژی پودری که با فشار دادن و پختن ساخته می شوند را می توان در حالت داغ بدون فرز به شکل فورج پودر درآورد. چگالی پودر آهنگری نزدیک به آهنگری معمولی است، با خواص مکانیکی خوب و دقت بالا، که می تواند پردازش برش بعدی را کاهش دهد. ساختار داخلی آهنگری پودری بدون جداسازی یکنواخت است و می توان از آن برای ساخت چرخ دنده های کوچک و سایر قطعات کار استفاده کرد. با این حال، قیمت پودر بسیار بالاتر از میله های معمولی است و کاربرد آن در تولید با محدودیت های خاصی همراه است. اعمال فشار استاتیک به فلز مایع ریخته شده در حفره قالب، که جامد می شود، متبلور می شود، جریان می یابد، دچار تغییر شکل پلاستیک می شود و تحت فشار شکل می گیرد، می تواند شکل و عملکرد مورد نیاز آهنگری قالب را به دست آورد. آهنگری فلزات مایع یک روش شکل دهی است که بین ریخته گری و آهنگری قرار دارد، به ویژه برای قطعات پیچیده با دیواره نازک که در آهنگری عمومی به سختی شکل می گیرند. علاوه بر مواد رایج مانند فولاد کربنی و فولاد آلیاژی با ترکیبات مختلف و به دنبال آن آلومینیوم، منیزیم، مس، تیتانیوم و آلیاژهای آنها، آلیاژهای تغییر شکل آلیاژهای با دمای بالا مبتنی بر آهن، آلیاژهای با دمای بالا مبتنی بر نیکل، و آلیاژهای با درجه حرارت بالا مبتنی بر کبالت نیز با آهنگری یا نورد تکمیل می شوند. با این حال، این آلیاژها دارای مناطق پلاستیکی نسبتاً باریکی هستند، بنابراین سختی آهنگری نسبتاً زیاد است. مواد مختلف دارای الزامات سختگیرانه برای دمای گرمایش، دمای باز کردن آهنگری و دمای آهنگری نهایی هستند.
جریان فرآیند آهنگری
روش های مختلف آهنگری فرآیندهای مختلفی دارند که در میان آنها فرآیند فورج قالب داغ طولانی ترین است و ترتیب کلی این است: برش بلانک فورج. گرمایش شمش آهنگری; آماده سازی رول فورج خالی; شکل گیری قالب فورج; لبه های برش؛ مشت زدن؛ تصحیح؛ بازرسی میانی، بررسی ابعاد و عیوب سطح آهنگری. عملیات حرارتی آهنگری برای از بین بردن استرس آهنگری و بهبود عملکرد برش فلز. تمیز کردن، عمدتا برای حذف مقیاس اکسید سطح. تصحیح؛ بازرسی: به طور کلی، آهنگری ها باید تحت بازرسی ظاهری و سختی قرار گیرند، در حالی که آهنگری های مهم نیز باید تحت تجزیه و تحلیل ترکیب شیمیایی، خواص مکانیکی، تست تنش باقیمانده و آزمایش های غیر مخرب قرار گیرند.
ویژگی های فورجینگ
در مقایسه با ریخته گری، فلز می تواند ریزساختار و خواص مکانیکی خود را پس از فرآوری آهنگری بهبود بخشد. پس از کار گرم و تغییر شکل به روش آهنگری، ساختار ریختهگری به دلیل تغییر شکل و تبلور مجدد فلز، از دندریتهای درشت و دانههای ستونی به ساختارهای تبلور مجدد هم محور با اندازههای ریزتر و یکنواخت تبدیل میشود. این امر باعث جدایی اولیه، تخلخل، تخلخل، ورود سرباره و سایر فشردگی و جوشکاری در شمش فولادی می شود و ساختار را فشرده تر می کند و انعطاف پذیری و خواص مکانیکی فلز را بهبود می بخشد. خواص مکانیکی قطعات ریخته گری کمتر از آهنگری از همان مواد است. علاوه بر این، پردازش آهنگری می تواند تداوم ساختار الیاف فلزی را تضمین کند و ساختار الیاف آهنگری را با شکل آهنگری مطابقت دهد. خط جریان فلزی کامل است، که می تواند تضمین کند که قطعات دارای خواص مکانیکی خوب و عمر طولانی هستند. آهنگری های تولید شده توسط آهنگری دقیق، اکستروژن سرد، اکستروژن گرم و سایر فرآیندها با ریخته گری قابل مقایسه نیستند. آهنگری اجسامی هستند که با تغییر شکل پلاستیکی شکل میگیرند تا زمانی که فلز تحت فشار قرار میگیرد، شکل مورد نیاز یا نیروی فشردهسازی مناسب را برآورده کند. این قدرت معمولاً از طریق استفاده از چکش یا فشار به دست می آید. فرآیند آهنگری ساختارهای ذرات بدیع را ایجاد می کند و خواص فیزیکی فلز را بهبود می بخشد. در استفاده عملی از قطعات، طراحی صحیح می تواند اطمینان حاصل کند که جریان ذرات در جهت فشار اصلی است. ریخته گری اجسام فلزی هستند که از روش های مختلف ریخته گری به دست می آیند، یعنی فلز مایع مذاب از طریق ریختن، تزریق، مکش یا سایر روش های ریخته گری به قالب های از پیش آماده شده تزریق می شود، سرد می شود و سپس در معرض ماسه برداری، تمیز کردن و پست قرار می گیرد. - درمان برای به دست آوردن اشیاء با شکل، اندازه و عملکرد خاص.
تجزیه و تحلیل سطح آهنگری
صنعت آهنگری چینی بر اساس معرفی، هضم و جذب فناوری خارجی توسعه یافته است. پس از سالها توسعه و تحول فناوری، سطح فنی شرکتها در این صنعت بسیار بهبود یافته است، از جمله طراحی فرآیند، فناوری آهنگری، فناوری عملیات حرارتی، فناوری ماشینکاری، آزمایش محصول و سایر جنبهها.
(1) تولیدکنندگان پیشرفته در طراحی فرآیند عموماً از فناوری شبیهسازی رایانهای پردازش داغ، طراحی فرآیند به کمک رایانه و فناوری مجازی استفاده میکنند و سطح طراحی فرآیند و قابلیتهای تولید محصول را بهبود میبخشند. معرفی و اعمال برنامه های شبیه سازی مانند DATAFOR، GEMARC/AUTOFORGE، DEFORM، LARSTRAN/SHAPE و THERMOCAL برای دستیابی به کنترل فرآیند طراحی کامپیوتر و پردازش حرارتی.
(2) اکثر پرس های هیدرولیک با تکنولوژی آهنگری 40MN و بالاتر مجهز به 100-400t هستند. متر اپراتورهای آهنگری اصلی و 20-40 تن. m اپراتورهای کمکی تعداد قابل توجهی از اپراتورها از کنترل کامپیوتری برای دستیابی به کنترل جامع فرآیند آهنگری استفاده می کنند که امکان کنترل دقت آهنگری در ± 3 میلی متر را فراهم می کند. اندازه گیری آنلاین آهنگری از دستگاه های اندازه گیری اندازه لیزری استفاده می کند.
(3) تمرکز فناوری عملیات حرارتی بهبود کیفیت محصول، افزایش کارایی عملیات حرارتی، صرفه جویی در انرژی و حفاظت از محیط زیست است. اگر فرآیند گرمایش کوره گرمایش و کوره عملیات حرارتی توسط رایانه کنترل شود، مشعل را می توان برای دستیابی به تنظیم خودکار احتراق، دمای کوره، احتراق خودکار و مدیریت پارامترهای گرمایش کنترل کرد. استفاده از گرمای زباله، کوره های عملیات حرارتی مجهز به محفظه های احتراق احیا کننده و غیره؛ با استفاده از مخازن روغن کوئنچ پلیمری با ظرفیت آلودگی کم و کنترل موثر خنک کننده، رسانه های مختلف کوئنچ بر پایه آب به تدریج جایگزین روغن خاموش کننده سنتی می شوند.
(4) نسبت ماشین آلات CNC در صنعت فناوری ماشینکاری به تدریج در حال افزایش است. برخی از موسسات این صنعت دارای مراکز ماشینکاری هستند و با توجه به انواع محصولات به ماشین آلات ماشینکاری اختصاصی مجهز می شوند، مانند مراکز ماشینکاری پنج مختصات، ماشین آلات ماشینکاری تیغه، آسیاب غلتکی، ماشین تراش غلتکی و غیره.
(5) اقدامات تضمین کیفیت: برخی از شرکت های داخلی خود را با آخرین ابزارهای تشخیص و فن آوری های آزمایش، سیستم های مدرن تست اولتراسونیک خودکار با پردازش داده های کنترل شده توسط کامپیوتر، و سیستم های مختلف تخصصی تست اولتراسونیک خودکار مجهز کرده اند تا گواهینامه سیستم های مختلف کیفیت را تکمیل کنند. تکنولوژی تولید کلیدی آهنگری های دنده سنگین با سرعت بالا به طور مداوم غلبه کرده است و بر این اساس تولید صنعتی حاصل شده است. بر اساس معرفی فناوری تولید پیشرفته و تجهیزات کلیدی از خارج از کشور، چین توانسته است به تنهایی تجهیزات تولیدی برای آهنگرهای دنده ای پرسرعت و سنگین را طراحی و تولید کند. این تجهیزات به سطح پیشرفته بین المللی نزدیک شده اند و بهبود سطح فناوری و تجهیزات به طور موثر توسعه صنعت آهنگری داخلی را ارتقا داده است.
اهمیت آهنگری
تولید آهنگری یکی از روش های اصلی فرآوری برای تهیه بلنک قطعات مکانیکی در صنعت ساخت مکانیکی است. با آهنگری نه تنها می توان شکل قطعات مکانیکی را به دست آورد، بلکه می توان ساختار داخلی فلز را نیز بهبود بخشید و خواص مکانیکی و فیزیکی فلز را افزایش داد. عموماً قطعات مکانیکی مهم با تنش و نیاز بالا با استفاده از روشهای تولید آهنگری ساخته میشوند. اجزای مهمی مانند محورهای توربین ژنراتور، روتورها، پروانهها، تیغهها، حلقههای نگهدارنده، ستونهای پرس هیدرولیک بزرگ، سیلندرهای فشار قوی، رولهای نورد فولادی، میل لنگ موتورهای احتراق داخلی، میلههای اتصال، چرخ دندهها، یاتاقانها و توپخانه در دفاع ملی صنعت همه از طریق آهنگری تولید می شود. [7] بنابراین، تولید آهنگری به طور گسترده در صنایعی مانند متالورژی، معدن، خودرو، تراکتور، ماشین آلات برداشت، نفت، صنایع شیمیایی، هوانوردی، هوافضا، سلاح و غیره استفاده می شود. حتی در زندگی روزمره، تولید آهنگری نیز نقش مهمی ایفا می کند. . به یک معنا، تولید سالانه آهنگری، نسبت آهنگری در کل خروجی آهنگری و همچنین اندازه و مالکیت تجهیزات آهنگری تا حدی سطح صنعتی یک کشور را منعکس می کند.