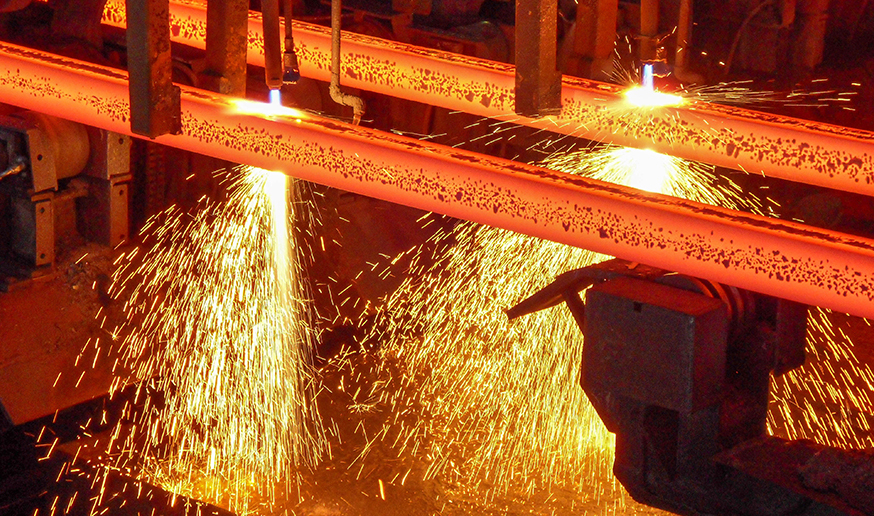
قابلیت ماشینکاری میله های گرد آلیاژ آهنگری بسته به ترکیب آلیاژ خاص و عملیات حرارتی متفاوت است. میله های گرد آلیاژی آهنگری می توانند ویژگی های ماشین کاری متفاوتی در مقایسه با سایر مواد مانند فولاد ضد زنگ یا فولاد کربنی داشته باشند. در اینجا چند فاکتور برای در نظر گرفتن وجود دارد:
ماشینکاری میله های گرد آلیاژی آهنگری عمیقاً تحت تأثیر ترکیب آلیاژ است. عناصر آلیاژی مانند کروم، مولیبدن و نیکل می توانند به طور قابل توجهی بر ماشین کاری تأثیر بگذارند. به عنوان مثال، کروم مقاومت در برابر خوردگی و سخت شدن را بهبود می بخشد، اما در صورت وجود در غلظت های بالا ممکن است سایش ابزار را افزایش دهد. مولیبدن استحکام و سختی پذیری را افزایش می دهد و باعث شکستن تراشه و کاهش سایش ابزار در حین ماشینکاری می شود. نیکل چقرمگی و مقاومت در برابر خوردگی را بهبود می بخشد، اما می تواند به سخت شدن کار و چالش در تشکیل تراشه کمک کند. برعکس، عناصری مانند تیتانیوم یا وانادیوم ممکن است استحکام و مقاومت در برابر سایش را بهبود بخشند، اما به دلیل تمایل آنها به سخت شدن در حین ماشینکاری، که نیاز به ابزار و استراتژی های تخصصی دارد، می توانند چالش هایی را ایجاد کنند.
میله های گرد آلیاژی آهنگری معمولاً سختی بالا و ریزساختار تصفیه شده را به دلیل فرآیند آهنگری نشان می دهند. در حالی که سختی بالا خواص مکانیکی مانند استحکام و مقاومت در برابر سایش را افزایش می دهد، همچنین می تواند در حین ماشینکاری چالش هایی ایجاد کند. سختی مواد بر شکل گیری تراشه، سایش ابزار و پرداخت سطح تأثیر می گذارد. ریزساختار، که تحت تأثیر عواملی مانند دمای آهنگری و سرعت خنکسازی قرار میگیرد، با تأثیر بر توزیع عناصر و فازهای آلیاژی در مواد، بر ماشینکاری تأثیر میگذارد.
رژیم عملیات حرارتی به کار گرفته شده در طول تولید به طور قابل توجهی بر قابلیت ماشینکاری میله های گرد آلیاژ آهنگری تأثیر می گذارد. عملیات حرارتی مانند بازپخت، کوئنچ و تمپر برای بهینه سازی خواص مکانیکی و در عین حال متعادل کردن قابلیت ماشینکاری استفاده می شود. بازپخت مواد را نرم می کند، سختی و تنش های داخلی را کاهش می دهد و در نتیجه ماشین کاری را بهبود می بخشد. برعکس، عملیات حرارتی نامناسب میتواند منجر به تغییرات ریزساختاری نامطلوب، مانند رسوب آستنیت یا کاربید باقیمانده شود که منجر به افزایش سایش ابزار و زبری سطح در حین ماشینکاری میشود.
کنترل تراشه موثر برای حفظ ثبات فرآیند و پایان سطح در عملیات ماشینکاری ضروری است. استراتژی های مناسب کنترل تراشه، مانند استفاده از تراشه شکن، کنترل ضخامت تراشه، و بهینه سازی تحویل مایع خنک کننده، برای جلوگیری از مسائل مربوط به تراشه مانند شکل گیری لبه های ساخته شده، پوشش ضعیف سطح و شکستگی ابزار بسیار مهم هستند. انتخاب هندسه ابزار برش مناسب، زاویه چنگک و سیال برش می تواند به بهینه سازی شکل گیری و تخلیه تراشه، بهبود ماشینکاری و بهره وری کمک کند.
اطمینان از پایداری قطعه کار برای دستیابی به دقت ابعاد، پرداخت سطح و عمر ابزار در عملیات ماشینکاری بسیار مهم است. برای به حداقل رساندن انحراف قطعه کار، ارتعاش و زنگ زدن در حین ماشینکاری، از سیستم های گیره، گیره و پشتیبانی دقیق استفاده می شود. تکنیکهای میرایی، مانند جاذبهای ارتعاش و میراگرهای جرمی تنظیمشده، ممکن است برای کاهش رزونانس و افزایش پایداری ماشینکاری، بهویژه زمانی که با میلههای گرد با قطر بزرگ یا اجزای جدار نازک سروکار داریم، مورد استفاده قرار گیرند.
روانکاری موثر و مدیریت خنک کننده برای کاهش اصطکاک، اتلاف گرما و افزایش عمر ابزار در حین ماشین کاری ضروری است. انتخاب و کاربرد مناسب سیالات برش، روان کننده ها و سیستم های خنک کننده به حداقل رساندن تولید گرما، سایش ابزار و زبری سطح کمک می کند و در عین حال تخلیه تراشه و پرداخت سطح را بهبود می بخشد. فنآوریهای پیشرفته خنککننده، مانند سیستمهای تحویل مایع خنککننده با فشار بالا و روغنکاری با حداقل مقدار (MQL)، قابلیتهای خنککننده و روغنکاری پیشرفتهتری را ارائه میدهند که ماشینکاری و بهرهوری را بیشتر بهبود میبخشد.3